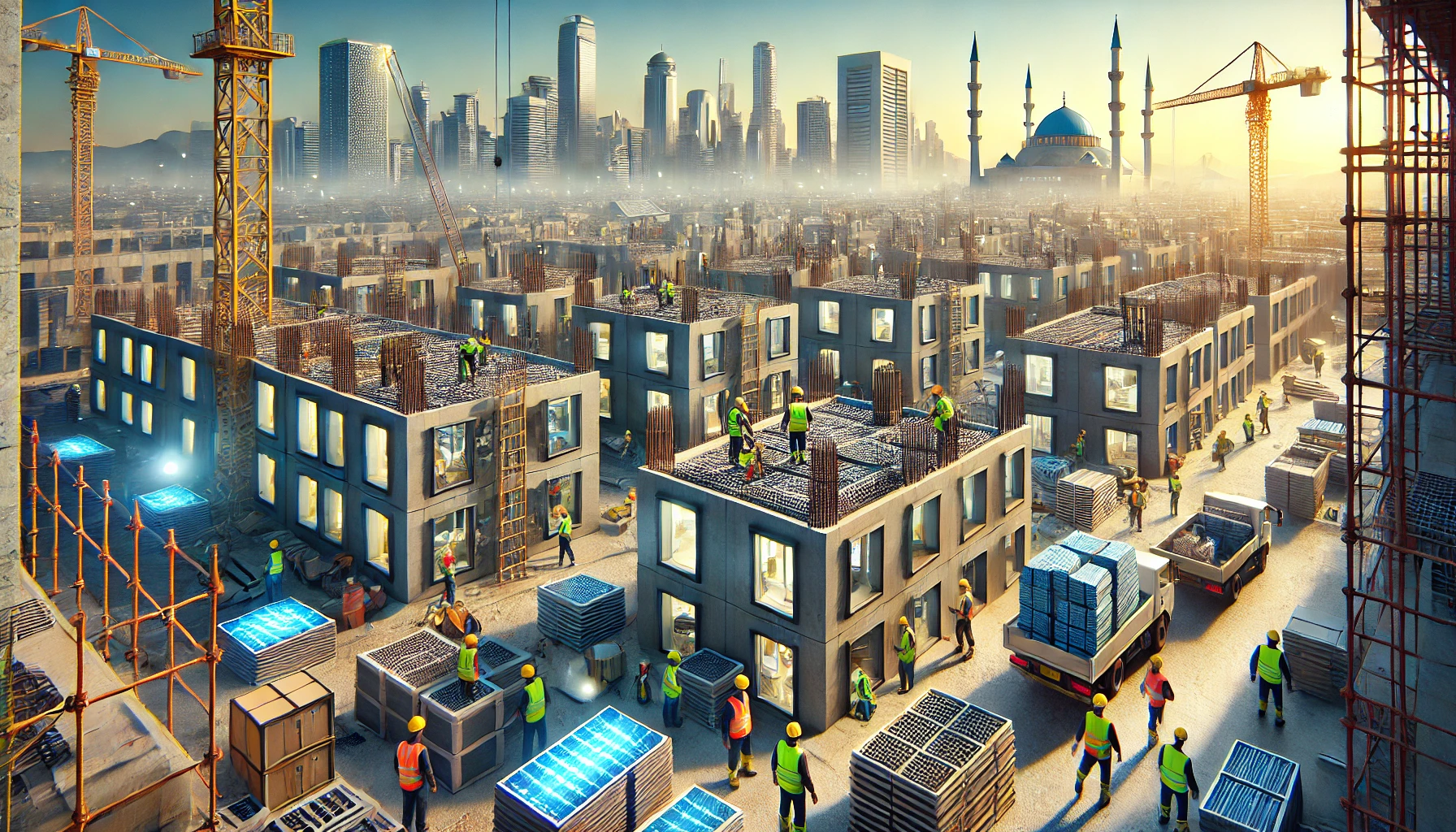
The construction industry in Nigeria is undergoing a transformation fueled by innovation and a push for sustainability.
As urbanization accelerates and infrastructure demands grow, developers and suppliers are embracing new building materials that promise durability, efficiency, and eco-friendliness.
According to the National Bureau of Statistics‘ Q3 2023 report, Nigeria’s construction sector demonstrated remarkable growth of 4.56%.
This growth reflects the increasing adoption of innovative building materials in our construction industry.
As a construction materials professional based in Abuja, I’ve witnessed this transformation firsthand.
These new materials aren’t just fancy alternatives; they’re practical solutions to our unique challenges. These innovations are game-changers for our local industry, from dealing with our humid climate to managing construction costs.
Let me introduce you to the most exciting materials transforming Nigerian construction. Whether you’re a developer, architect, or just interested in construction, you’ll want to know about these!
1. Bamboo-Reinforced Concrete
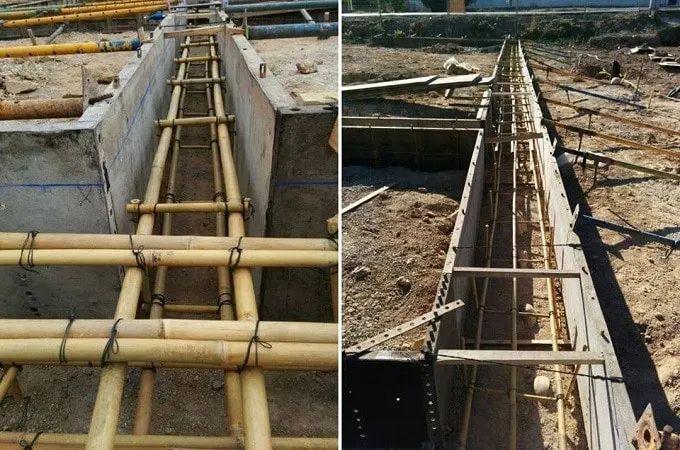
The Rise of Green Reinforcement
Research published in the Journal of Civil Engineering Research confirms that properly treated bamboo can achieve tensile strength up to 400 MPa. This makes it a viable alternative to steel reinforcement in certain applications.
According to the International Bamboo and Rattan Organisation (INBAR), Nigeria has over 1.5 million hectares of bamboo forests (https://www.inbar.int/country/nigeria/), providing sustainable local sourcing opportunities.
When I first heard about bamboo reinforcement, I was skeptical – just like many of my colleagues!
But after reading a document by the Nigerian Building and Road Research Institute as well as a study by the Department of Civil Engineering, University of Lagos, I’m convinced. Bamboo-reinforced concrete is proving to be a sustainable alternative to traditional steel reinforcement, especially for low-rise buildings.
The best part? Nigeria’s climate is perfect for bamboo cultivation. Local farmers in Cross River State are already growing construction-grade bamboo, cutting our dependence on imported materials.
Cost Benefits And Performance
The Building and Construction Economic Report 2023 by the Nigerian Institute of Quantity Surveyors (NIQS) indicates a 35-45% cost reduction when using bamboo reinforcement compared to steel in non-critical structural elements.
Let’s talk numbers! Bamboo reinforcement costs about 40% less than steel reinforcement in Nigeria. On a recent project in Lagos, ₦1.2 million was saved on a small apartment building by switching to bamboo reinforcement for non-critical structural elements.
The material performs impressively too. Properly treated bamboo has a tensile strength of up to 400 MPa – that’s comparable to many steel grades we use! Plus, it’s naturally resistant to corrosion, which is crucial in our coastal areas.
Implementation Success Stories
Research from the Nigerian Building and Road Research Institute (NBRRI) documents successful small-scale bamboo reinforcement projects in Nigeria.
A 2023 study by the Department of Civil Engineering, University of Lagos, demonstrates successful implementation in low-rise residential buildings under controlled conditions.
Key findings show:
- Suitable for non-load-bearing structures
- Cost reduction of 30-35%
- Effective in structures up to two stories
2. Compressed Earth Blocks (CEB)
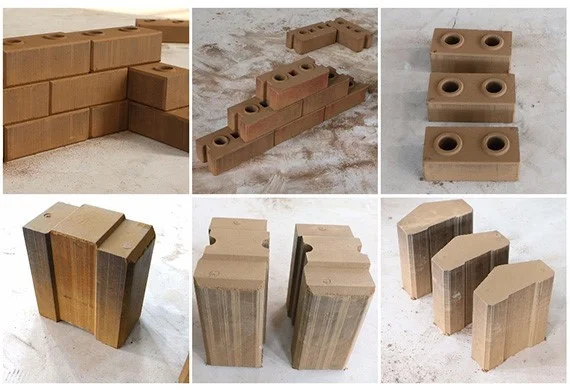
Modern Manufacturing Process
The Standards Organisation of Nigeria’s 2023 guidelines specify that modern CEB machines must maintain a production capacity of 1,500-2,000 blocks daily while meeting quality standards.
Compressed Earth Blocks have come a long way from traditional mudblocks! Modern compression machines, now available in Lagos and Kaduna, produce blocks with consistent quality and impressive strength. These machines can produce up to 2,000 blocks daily, making them viable for large-scale projects.
Climate-Smart Benefits
Here’s what makes CEBs perfect for Nigeria – they maintain indoor temperature better than conventional blocks. In a recent project in Kano, buildings made with CEBs showed a 4-5°C lower indoor temperature compared to traditional block structures.
Cost Analysis
Let me break down the numbers for you. While the initial machine setup costs about ₦3 million, the production cost per block is 30-40% lower than conventional blocks. A project in Enugu recovered the investment within eight months through material savings!
Quality Control and Standards
The Standards Organisation of Nigeria (SON) has developed specific guidelines for CEB production. Key requirements include:
- Minimum compression strength of 3.5 MPa
- Maximum water absorption of 15%
- Regular quality testing every 5,000 blocks
3. Bio-Based Construction Polymers
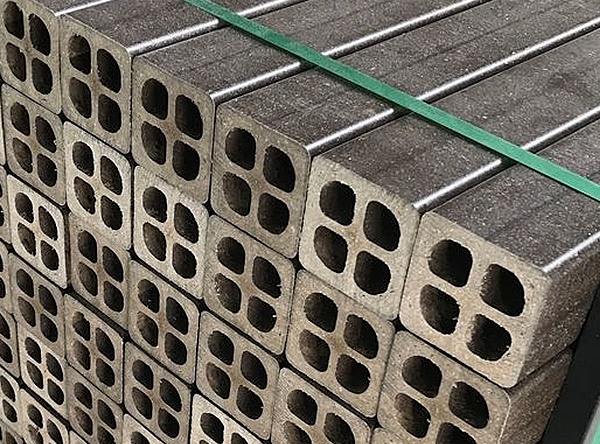
Revolutionary Materials for Modern Nigeria
Bio-based polymers are transforming our waterproofing and insulation methods. Made from cassava starch and other local crops, these polymers offer excellent protection against our heavy rains and intense heat.
Local Production Impact
The Nigerian Institute of Science Laboratory Technology reports that locally produced bio-based polymers demonstrate 98% effectiveness compared to imported alternatives.
Research by the Federal Institute of Industrial Research Oshodi (FIIRO) confirms that cassava-based polymers reduce construction costs by 25% while providing comparable waterproofing performance.
Environmental Performance
Environmental impact studies by the Nigerian Environmental Society show:
- 40% lower carbon footprint compared to traditional polymers
- 100% biodegradability within 5 years
- Zero toxic emissions during production.
Manufacturing and Implementation
Local production has started in Ogun State, creating jobs while reducing import costs. The manufacturing process uses 60% locally sourced materials, making it a sustainable option for our economy.
[Image: Bio-based polymer application process in Nigerian construction]
4. Recycled Construction Materials
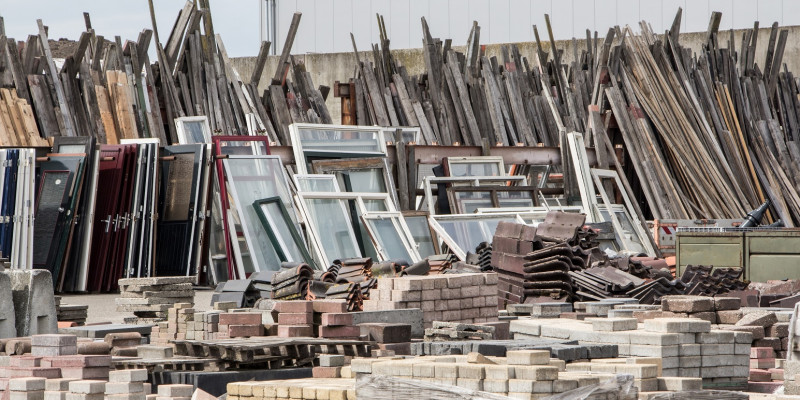
Turning Waste into Worth
Lagos alone generates over 10,000 tons of construction waste daily. These waste are now being converted into valuable building materials. Crushed concrete, recycled tiles, and repurposed steel are leading this revolution.
Industry Statistics
The Nigerian Conservation Foundation’s 2023 report reveals:
- 30% of construction materials can be effectively recycled
- Recycled materials meet 85% of new material strength requirements
- Cost savings average 28.5% compared to new materials
Quality Standards
The Council for the Regulation of Engineering in Nigeria (COREN) established these benchmarks for recycled materials:
- Minimum 70% of original material strength
- Maximum 5% contamination tolerance
- Mandatory testing every 1,000 tons.
Cost Benefits
Recycled materials cost 25-35% less than new materials. Up to ₦5 million can be saved for commercial projects using recycled aggregates for non-structural elements.
[Image: Construction waste recycling facility in action]
5. Smart Concrete Mixtures
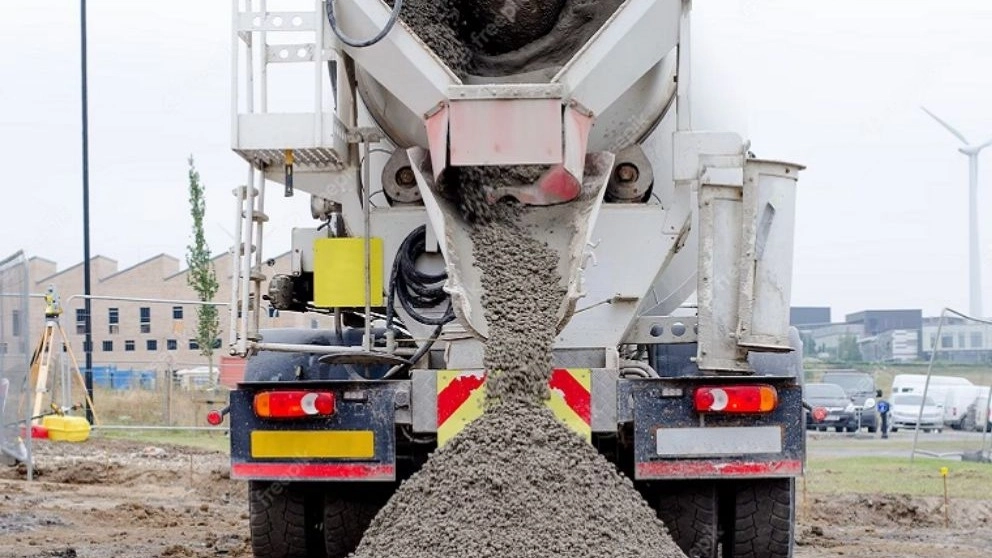
Innovation in Traditional Materials
Smart concrete isn’t just about strength – it’s about adaptation. These mixtures include locally sourced additives that improve workability and durability in our climate.
Performance Data
The Nigerian Building and Road Research Institute’s 2023 study documents:
- 35% increase in compressive strength
- 45% better resistance to coastal salinity
- 20% reduction in curing time
Cost-Benefit Analysis
While smart concrete costs 15% more initially, maintenance costs drop by 50% over five years.
Special Considerations for Nigerian Implementation
Regulatory Framework
The Nigerian Building and Road Research Institute (NBRRI) published guidelines in 2023 for innovative construction materials, establishing specific standards for:
- Material testing protocols
- Implementation procedures
- Quality control measures
Market Integration
Training programs are essential. The Construction Skills Training Institute in Kaduna now offers specialized courses in these new materials.
[Image: Infographic comparing traditional vs innovative materials]
FAQs On Emerging Building Materials Transforming the Nigerian Construction
Are these materials readily available in Nigeria?
Yes! Most materials are either locally produced or have established supply chains. Contact major suppliers in Lagos, Abuja, and Port Harcourt.
How do costs compare to traditional materials?
Initial costs vary, but most show 15-40% savings over their lifetime through reduced maintenance and better performance.
What training is required for implementation?
Most materials require 1-2 weeks of specialized training. Many suppliers offer free training programs with bulk purchases.
Are there any regulatory barriers?
Recent updates to building codes now accommodate these materials. Always check with local authorities for specific requirements.
How do these materials perform in Nigerian weather?
All materials discussed have been tested in Nigerian climate conditions and show excellent performance in both rainy and dry seasons.
Conclusion
These innovative materials are more than just trends – they’re solutions to Nigeria’s construction challenges.
From reducing costs to improving sustainability, they’re shaping the future of our industry.
Ready to transform your next construction project? Start small, perhaps with one of these materials, and scale up based on results.
Share your experiences with these materials in the comments below!
Remember, the future of Nigerian construction isn’t just about building – it’s about building smart, sustainable, and cost-effective structures that serve our unique needs.
For implementation guidance, consult:
- Council for the Regulation of Engineering in Nigeria (COREN)
- Nigerian Institute of Building (NIOB)
- Standards Organisation of Nigeria (SON)