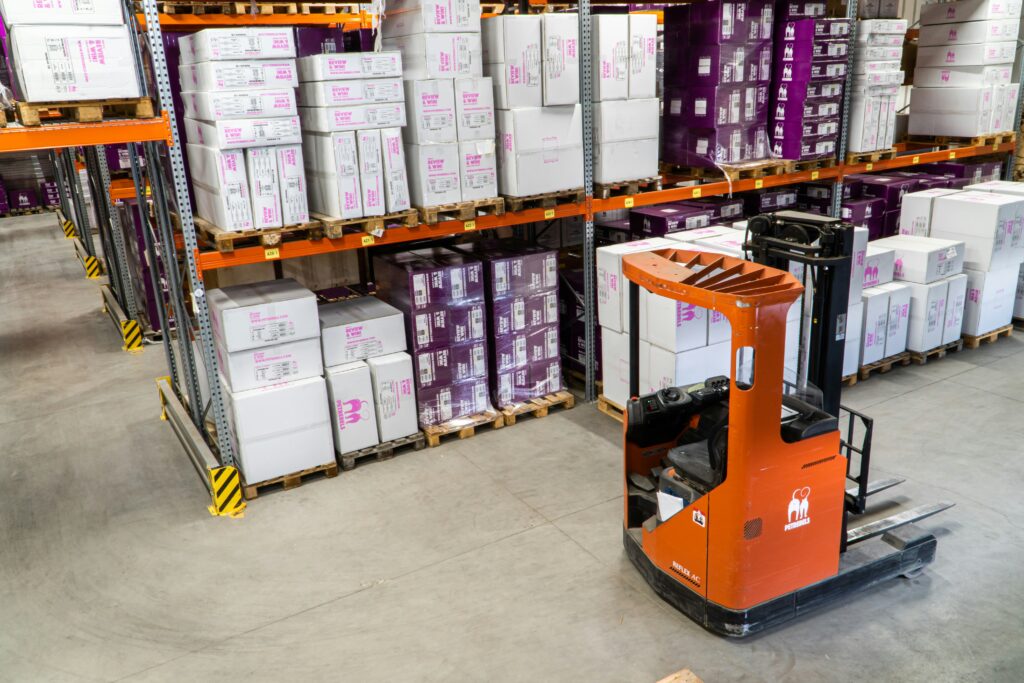
Tired of juggling spreadsheets and struggling to keep track of your construction supplies? You’re not alone!
Did you know that 61% of construction firms still rely on manual processes for inventory management?
It’s time to embrace the cloud revolution! In this article, we’ll explore the top cloud-based inventory software solutions tailored for construction suppliers.
To help decide, here’s a list of 5 Best Cloud-Based Inventory Solutions for Construction Suppliers based on ideal business type, key features, pricing and more.
Let’s dive into how this technology is reshaping the construction landscape in 2024!
What Are The Best Cloud-based Inventory Software?
Here are my top picks for the best cloud-based inventory software for construction suppliers!
ProCore Inventory Management
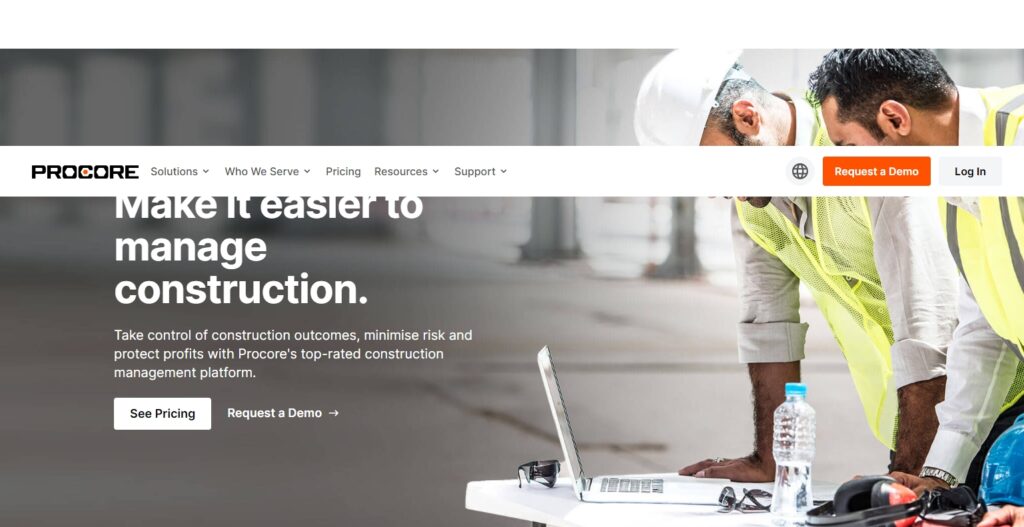
Ideal for: Large-scale operations and enterprise-level construction suppliers
Key features:
- Comprehensive construction ERP integration
- Real-time stock updates across multiple locations
- Advanced inventory forecasting tools
- Supplier relationship management portal
- IoT-enabled inventory tracking for high-value items
Pros:
- Robust reporting and analytics capabilities
- Excellent scalability for growing businesses
- Strong mobile app for on-site inventory management
Cons:
- Steep learning curve
- Higher price point compared to other solutions.
Acctivate Inventory Software
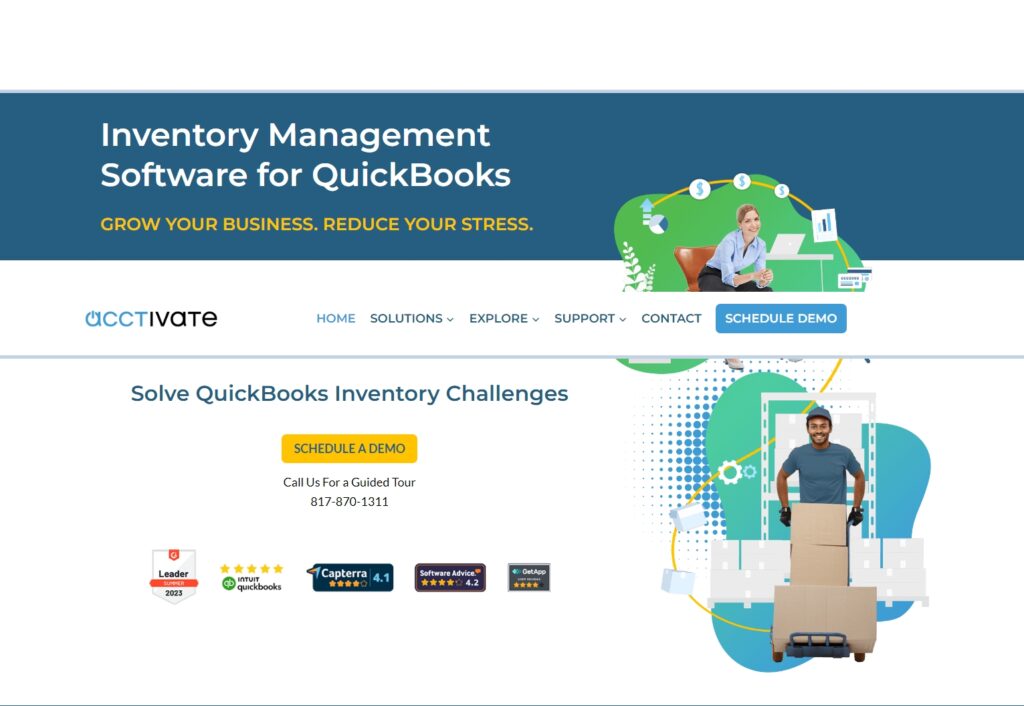
Ideal for: Small to medium-sized construction suppliers
Key features:
- User-friendly interface with intuitive navigation
- Barcode scanning for efficient building supplies tracking
- Integration with popular accounting software
- Just-in-time inventory management for construction materials
- Custom reporting tools
Pros:
- Affordable pricing structure
- Excellent customer support
- Easy implementation and data migration
Cons:
- Limited advanced features compared to enterprise solutions
- May require add-ons for full functionality.
Fishbowl Inventory
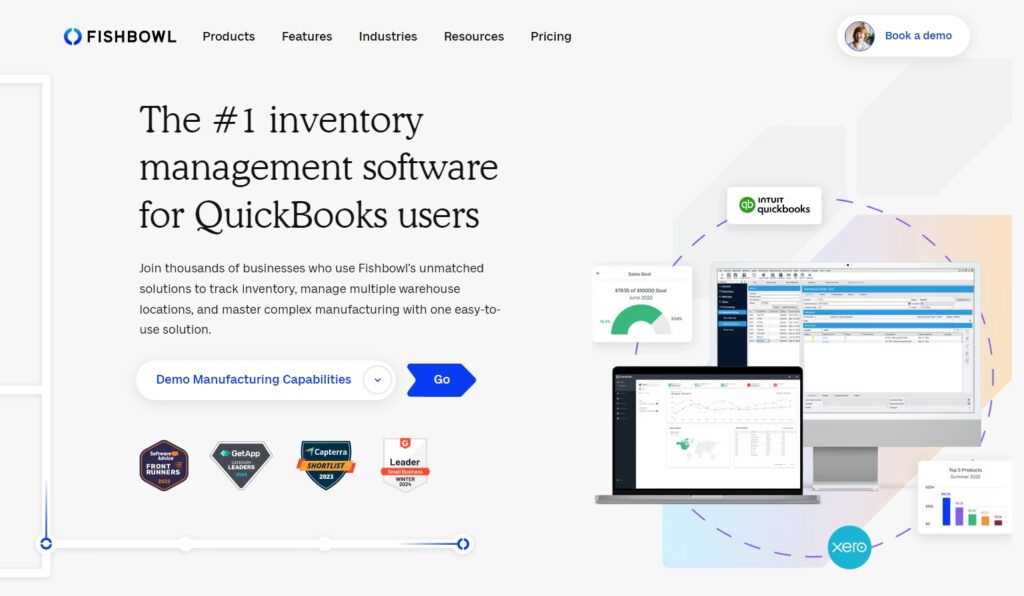
Ideal for: Construction suppliers focusing on manufacturing and distribution
Key features:
- Robust multi-location stock control
- Advanced bill of materials and kitting capabilities
- Integration with QuickBooks and other accounting platforms
- Automated reordering based on stock-level alerts
- Customizable workflows for unique business processes
Pros:
- Strong manufacturing features for suppliers who create custom products
- Excellent inventory optimization tools
- Comprehensive training resources available
Cons:
- Mobile app functionality could be improved
- Some users report occasional performance issues with large datasets
Sortly Pro
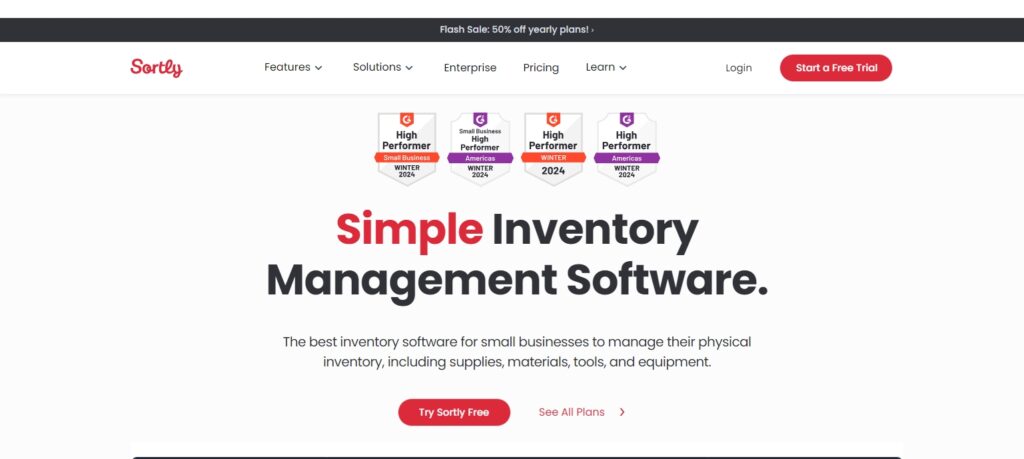
Ideal for: Construction suppliers prioritizing ease of use and mobile accessibility
Key features:
- Intuitive mobile inventory app for construction
- QR code and barcode scanning capabilities
- Cloud-based asset tracking with photo documentation
- Customizable fields for detailed item information
- Low-stock alerts and reordering reminders
Pros:
- Extremely user-friendly interface
- Affordable pricing for small businesses
- Excellent for visual inventory management
Cons:
- Limited advanced reporting features
- May lack some integrations needed for larger operations
Cin7 Inventory Management
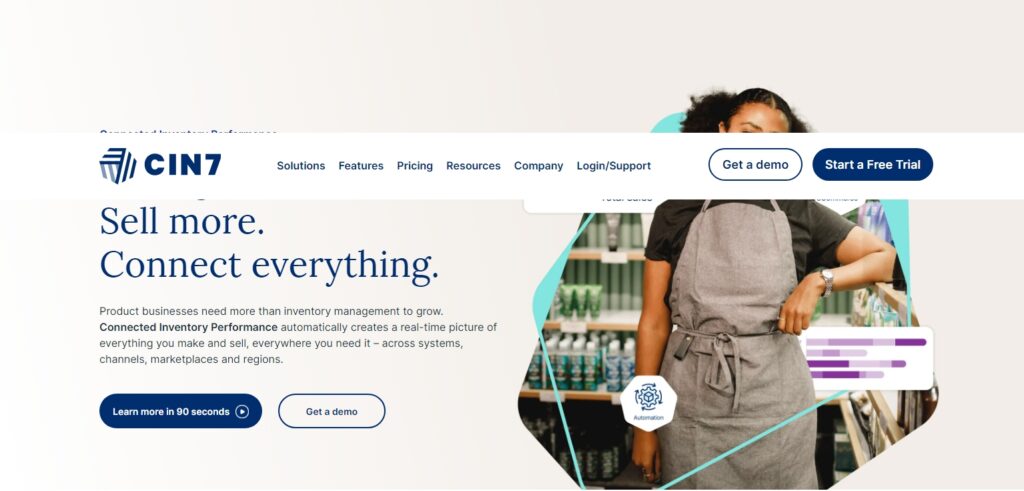
Ideal for: Construction suppliers with complex supply chain needs
Key features:
- Advanced supply chain visibility software
- Multi-channel inventory management
- Powerful demand planning and forecasting tools
- EDI capabilities for streamlined supplier communications
- Comprehensive API for custom integrations
Pros:
- Excellent for businesses with both B2B and B2C sales channels
- Strong inventory lifecycle management features
- Regular updates and new feature releases
Cons:
- Can be complex to set up and configure
- A higher price point may not be suitable for smaller suppliers
Remember, the right inventory management system can significantly improve your supply chain efficiency, reduce costs, and enhance customer satisfaction.
Take the time to thoroughly evaluate each option, possibly through free trials or demos, before making your final decision.
What is Cloud-based Inventory Software for Construction?
Cloud-based inventory software for construction is a digital solution that revolutionizes how construction firms manage their materials, equipment, and assets.
Unlike traditional on-premise systems, this software leverages cloud technology to provide real-time inventory tracking and management capabilities accessible from anywhere with an internet connection.
At its core, cloud inventory software for construction is designed to streamline the complex task of construction resource management.
It offers a centralized platform where contractors, project managers, and site supervisors can monitor, track, and control their inventory across multiple projects and locations.
When choosing the best cloud-based inventory software for your construction supply business, consider factors such as:
- Scalability: Ensure the solution can grow with your business
- Integration capabilities: Look for software that works well with your existing tools
- Mobile accessibility: On-site inventory updates are crucial in the construction industry
- Customization options: Your business is unique, and your software should adapt to your needs
- Cost-effectiveness: Balance features with your budget constraints
- User-friendliness: Choose a solution that your team can quickly adopt and efficiently use
Why Cloud-Based Inventory Software is a Game-Changer
The construction industry is evolving rapidly, and cloud-based inventory software is at the forefront of this digital transformation.
Let’s dive into the reasons why this technology is revolutionizing the way construction suppliers manage their inventory.
Real-Time Data Access and Collaboration
- Instant updates: Cloud inventory management systems provide real-time stock updates, ensuring that everyone in your organization has access to the most current information.
- Improved teamwork: Multiple team members can access and update inventory data simultaneously, fostering better collaboration and reducing communication gaps.
- On-site accessibility: With mobile inventory apps for construction, your team can check stock levels and update information directly from job sites.
Cost-Effectiveness and Scalability
- Reduced IT costs: Cloud-based solutions eliminate the need for expensive on-premise hardware and dedicated IT staff to maintain the system.
- Pay-as-you-grow model: Many cloud inventory solutions offer scalable pricing, allowing you to start small and expand as your business grows.
- Automatic updates: Software updates and new features are rolled out automatically, ensuring you always have access to the latest tools without additional costs.
Enhanced Accuracy and Reduced Human Error
- Automated data entry: Barcode scanning for building supplies and RFID inventory for construction minimize manual data entry errors.
- Intelligent forecasting: Advanced inventory forecasting tools use historical data and AI to predict future stock needs more accurately than human estimates.
- Standardized processes: Cloud systems enforce consistent procedures across your organization, reducing discrepancies and improving overall accuracy.
Improved Supply Chain Visibility
- End-to-end tracking: Cloud-based inventory software provides complete supply chain visibility, from supplier to end customer.
- Supplier relationship management: Integrated portals allow for better communication and coordination with your suppliers.
- Demand planning: Real-time data enables more accurate construction supply demand planning, helping you optimize stock levels.
Integration Capabilities
- Seamless connectivity: Cloud inventory systems often integrate easily with other business tools, such as construction ERP solutions and accounting software.
- Data centralization: By connecting various systems, you create a single source of truth for all your inventory and business data.
- API accessibility: Many cloud solutions offer APIs, allowing for custom integrations with other tools specific to your business needs.
Enhanced Security and Data Protection
- Robust security measures: Cloud providers invest heavily in security, often providing better protection than most businesses could afford on their own.
- Automatic backups: Cloud inventory security includes regular data backups, ensuring your critical information is safe and recoverable.
- Disaster recovery: In case of local disasters, your data remains safe and accessible in the cloud.
Improved Customer Satisfaction
- Faster response times: With real-time inventory data, you can quickly inform customers about product availability and delivery times.
- Reduced stockouts: Better inventory management leads to fewer stockouts, ensuring you can meet customer demands consistently.
- Personalized service: Access to detailed inventory data allows you to offer more personalized recommendations and solutions to your customers.
Data-Driven Decision Making
- Advanced analytics: Cloud-based systems often come with powerful inventory analytics for suppliers, helping you make informed decisions.
- KPI tracking: Easily monitor key performance indicators (KPIs) related to inventory turnover, carrying costs, and other crucial metrics.
- Trend identification: Historical data analysis can reveal patterns and trends, enabling proactive inventory management.
Environmental Benefits
- Reduced paper usage: Digital inventory tracking significantly reduces the need for paper-based records.
- Optimized logistics: Better inventory management can lead to more efficient transportation and reduced carbon footprint.
- Waste reduction: Accurate demand forecasting helps minimize overstock situations and reduce waste of construction materials.
Future-Proofing Your Business
- IoT readiness: Many cloud inventory systems are prepared to integrate with IoT-enabled inventory tracking devices as they become more prevalent in the construction industry.
- Artificial Intelligence: As AI technology advances, cloud-based systems are well-positioned to incorporate these innovations for even smarter inventory management.
- Adaptability: Cloud solutions are continuously evolving, ensuring your business can quickly adapt to new industry trends and requirements.
In conclusion, cloud-based inventory software is not just a trend – it’s a fundamental shift in how construction suppliers manage their operations.
By embracing this technology, you’re not only solving today’s inventory challenges but also positioning your business for future success in an increasingly digital world.
The combination of real-time data, improved accuracy, cost-effectiveness, and enhanced collaboration makes cloud-based inventory software a true game-changer in the construction supply industry.
Don’t get left behind – it’s time to build a stronger, more efficient business with the power of the cloud!
Key Features to Look for in Construction Inventory Software
When selecting the ideal cloud-based inventory software for your construction supply business, it’s crucial to identify the features that will have the most significant impact on your operations.
Here’s a comprehensive breakdown of the essential features to consider:
Multi-Location Inventory Tracking
- Real-time sync: Ensure your software offers seamless synchronization across all your warehouses and job sites.
- Transfer management: Look for easy-to-use tools for managing stock transfers between locations.
- Location-specific reporting: The ability to generate reports for individual locations or compare across multiple sites is invaluable.
Integration Capabilities
- Accounting software integration: Seamless connection with popular accounting tools like QuickBooks or Xero for accurate financial reporting.
- Project management integration: Look for software that can interface with construction project management tools to align inventory with project needs.
- CRM integration: Connecting your inventory system with customer relationship management software can enhance sales and service processes.
Mobile Accessibility
- User-friendly mobile app: A robust mobile inventory app for construction is essential for on-site updates and checks.
- Offline functionality: The ability to work offline and sync later is crucial for construction sites with poor internet connectivity.
- Mobile scanning: Look for apps that support barcode and QR code scanning using smartphone cameras.
Advanced Tracking Technologies
- Barcode scanning for building supplies: This feature dramatically speeds up data entry and reduces errors.
- RFID inventory for construction: Radio-frequency identification can be especially useful for tracking high-value items or large quantities of materials.
- IoT-enabled inventory tracking: Some advanced systems offer integration with Internet of Things sensors for real-time monitoring of stock levels and conditions.
Automated Reordering and Stock Level Alerts
- Customizable reorder points: The ability to set automatic reorder triggers based on minimum stock levels.
- Supplier lead time consideration: Smart systems that factor in supplier lead times when suggesting reorder quantities.
- Low stock notifications: Automated alerts when inventory items fall below specified thresholds.
Reporting and Analytics
- Customizable dashboards: Look for software that allows you to create tailored dashboards for at-a-glance insights.
- Inventory turnover analysis: Tools to help you optimize your stock levels and identify slow-moving items.
- Forecasting capabilities: Advanced inventory forecasting tools that use historical data to predict future needs.
Supplier Management
- Supplier database: A centralized system for managing supplier information and performance metrics.
- Purchase order automation: Features that streamline the PO process based on inventory levels and supplier data.
- Supplier portal: A dedicated interface for suppliers to view orders, update shipping information, and manage their accounts.
Cost Tracking and Valuation
- Multiple costing methods: Support for various inventory valuation methods (FIFO, LIFO, average cost, etc.).
- Real-time inventory valuation: Ability to get up-to-date valuations of your entire inventory at any time.
- Cost history tracking: Features that allow you to monitor price changes over time for better negotiation and budgeting.
Batch and Serial Number Tracking
- Lot control: Essential for managing materials with expiration dates or those subject to recalls.
- Serial number tracking: Crucial for high-value items and warranty management.
- Traceability reports: The ability to quickly trace items back to their source or forward to their final destination.
User Access Control and Audit Trails
- Role-based access: Customize user permissions based on job roles and responsibilities.
- Activity logging: Detailed audit trails to track who made changes to inventory records and when.
- Electronic signatures: Support for e-signatures to enhance accountability and comply with regulatory requirements.
Customization and Flexibility
- Custom fields: The ability to add unique identifiers or attributes to inventory items.
- Workflow customization: Features that allow you to tailor the software to your specific business processes.
- API access: Look for systems with robust APIs that allow for custom integrations and extensions.
Inventory Optimization Tools
- ABC analysis: Features that help categorize inventory items based on their value and usage frequency.
- Safety stock calculation: Tools to help determine optimal safety stock levels based on demand variability.
- Excess stock identification: Reports that highlight overstocked items to prevent tied-up capital.
Customer Order Management
- Order tracking: Features that link customer orders directly to inventory for real-time availability checks.
- Backorder management: Tools to efficiently manage and fulfill backorders as stock becomes available.
- Customer-specific pricing: The ability to set and manage different price levels for various customer types.
Reporting and Compliance
- Customizable report builder: Look for software that allows you to create tailored reports for different stakeholders.
- Compliance reporting: Features that help you meet industry-specific regulatory requirements.
- Scheduled reporting: The ability to automate regular report generation and distribution.
Data Security and Backup
- Cloud inventory security: Robust encryption and security measures to protect your sensitive data.
- Regular backups: Automatic and frequent data backups to prevent loss of critical information.
- Data recovery options: Easy-to-use tools for restoring data in case of accidental deletions or system failures.
When evaluating construction inventory software, prioritize these features based on your specific business needs.
Remember, the goal is to find a solution that not only addresses your current challenges but also supports your future growth.
With the right cloud-based inventory system in place, you’ll be well-equipped to streamline operations, reduce costs, and stay competitive in the fast-paced construction supply industry.
All the software companies have demos or trials, so don’t hesitate to request demos or trials from potential software providers to ensure the features work as expected in real-world scenarios.
The right inventory management solution can be a powerful tool in transforming your construction supply business for the digital age!
ROI and Long-Term Benefits of Cloud Inventory Management
Investing in cloud-based inventory software is a strategic decision that can yield significant returns and long-term benefits for construction suppliers.
Let’s dive into the specifics of how this technology can impact your bottom line and future-proof your business.
Quantifiable ROI Metrics
- Inventory Carrying Cost Reduction:
- Cloud systems optimize stock levels, reducing excess inventory
- Typical savings: 20-30% reduction in carrying costs
- Example: A supplier with $1M in inventory could save $200,000-$300,000 annually
- Labor Cost Savings:
- Automation reduces manual data entry and physical counting time
- Average time savings: 40-60% on inventory-related tasks
- Example: If inventory management takes 100 hours/week, you could save 40-60 hours, equating to $40,000-$60,000 annually (at $20/hour)
- Stockout Prevention:
- Real-time tracking and automated reordering minimize stockouts
- Potential increase in sales: 5-10% due to improved product availability
- Example: For $5M annual revenue, this could mean an additional $250,000-$500,000 in sales
- Improved Inventory Turnover:
- Better forecasting and demand planning increase inventory turns
- Average improvement: 20-30% increase in turnover ratio
- Impact: Faster cash conversion cycle and improved cash flow
Long-Term Strategic Benefits
- Enhanced Decision Making:
- Real-time data and advanced analytics enable data-driven decisions
- Benefit: More accurate demand forecasting and strategic planning
- Scalability for Growth:
- Cloud solutions easily scale with your business
- Advantage: No need for costly system overhauls as you expand
- Improved Customer Satisfaction:
- Faster order fulfillment and fewer stockouts lead to happier customers
- Result: Increased customer loyalty and positive word-of-mouth
- Competitive Advantage:
- Efficient operations allow for more competitive pricing and service
- Outcome: Increased market share and stronger industry position
Operational Efficiency Gains
- Streamlined Procurement Process:
- Automated purchase orders and supplier management
- Benefit: 30-50% reduction in procurement cycle time
- Improved Accuracy:
- Barcode scanning and RFID reduce human error
- Typical improvement: 99%+ inventory accuracy (up from 70-80% manual)
- Enhanced Supplier Relationships:
- Better forecasting allows for more accurate orders and timely payments
- Result: Potential for better pricing and terms from suppliers
Financial Impact
- Reduced Working Capital Requirements:
- Optimized inventory levels free up cash
- Potential impact: 20-30% reduction in working capital tied up in inventory
- Improved Cash Flow:
- Faster inventory turns and reduced carrying costs improve cash flow
- Benefit: More cash available for investments or debt reduction
- Better Financial Planning:
- Accurate, real-time inventory valuation aids in financial reporting
- Advantage: More precise budgeting and forecasting
Risk Mitigation
- Theft and Loss Prevention:
- Detailed tracking reduces shrinkage
- Average reduction: 20-40% in inventory shrinkage
- Compliance and Auditing:
- Automated tracking and reporting simplify audits
- Benefit: Reduced risk of non-compliance penalties
- Disaster Recovery:
- Cloud-based systems offer better data protection and recovery
- Advantage: Minimized risk of data loss and business interruption
Case Studies and Success Stories
- Mid-Size Construction Supplier:
- Implemented cloud inventory system in 2022
- Results after one year:
- 25% reduction in inventory carrying costs
- 35% improvement in order fulfillment speed
- 15% increase in sales due to better stock availability
- ROI: The system paid for itself within 8 months
- Large Building Materials Distributor:
- Switched to a cloud-based solution in 2021
- Two-year impact:
- 40% reduction in stockouts
- 50% decrease in time spent on inventory counts
- 20% improvement in supplier delivery performance
- ROI: 300% return on investment over two years
Future-Proofing Your Business
- IoT Integration Readiness:
- Cloud systems easily integrate with emerging IoT technologies
- Benefit: Prepared for future advancements in inventory tracking
- AI and Machine Learning Capabilities:
- Many cloud solutions are incorporating AI for predictive analytics
- Advantage: Continuously improving forecasting and optimization
- Sustainability Improvements:
- Better inventory management reduces waste and improves sustainability
- Impact: Meeting growing customer and regulatory demands for eco-friendly practices
Calculating Your Potential ROI
To estimate your potential ROI:
- Assess current costs:
- Inventory carrying costs
- Labor costs for inventory management
- Losses from stockouts and overstocking
- Estimate potential savings based on industry averages:
- 20-30% reduction in carrying costs
- 40-60% reduction in inventory management labor
- 5-10% increase in sales due to better stock availability
- Factor in the cost of the cloud system:
- Software licensing fees
- Implementation and training costs
- Ongoing support and maintenance
- Calculate ROI: ROI = (Gain from Investment – Cost of Investment) / Cost of Investment
Example:
- Current annual inventory-related costs: $1,000,000
- Estimated savings and gains: $300,000
- Cost of cloud system (first year): $50,000
- ROI = ($300,000 – $50,000) / $50,000 = 500%
In conclusion, the ROI and long-term benefits of cloud inventory management for construction suppliers are substantial and multifaceted.
From immediate cost savings and efficiency gains to long-term strategic advantages, the impact can be transformative.
While the initial investment and implementation process may seem daunting, the potential returns far outweigh the costs for most businesses.
As you consider making the switch to a cloud-based inventory system, remember that the benefits extend beyond mere numbers.
You’re investing in a platform that will help your business stay competitive, agile, and prepared for future challenges and opportunities in the ever-evolving construction industry.
The question isn’t whether you can afford to implement cloud inventory management – it’s whether you can afford not to.
The Best Cloud-based Inventory Software for 2024: Final Thoughts
If you’re still with us, thank you for reading through this guide to the best web hosting services of 2024.
Ready to revolutionize your construction supply business? The right cloud-based inventory software can be a total game-changer!
I think the verdict is clear:
- If you operate large-scale operations and enterprise-level construction suppliers: Get ProCore. Its Real-time stock updates across multiple locations coupled with its robust reporting and analytics capabilities make it an ideal fit.
- If you run small to medium-sized construction suppliers: Get Acctivate. Its barcode scanning for efficient building supplies tracking and affordable pricing structure gives it an edge for your small business.
- If your model is construction suppliers focusing on manufacturing and distribution: Fishbowl is what you get. Its strong manufacturing features for suppliers who create custom products make it the go-to software for such models.
- If your priority is ease of use and mobile accessibility for construction suppliers: Get Sortly Pro. It has an intuitive mobile inventory app that is extremely user-friendly.
- If you operate a construction suppliers business with complex supply chain needs: Get Cin7. It has advanced supply chain visibility capabilities. Excellent for businesses with both B2B and B2C sales channels.
Take the first step towards revolutionizing your building materials business today by exploring the options we’ve discussed. Your future self will thank you for it!